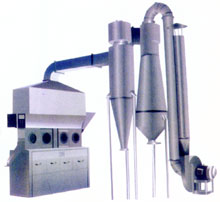
Brief introduction:
Boiling dryer is also called as fluidized bed. Having been used for more than 20 years since 1963, it has been improved constantly and has played more and more part in the industry of pharmacy, chemical industry, food, grain and so on. It is composed by air filter, heater, fluidized bed main machine, feeder, cyclone separator, cloth bag duster, high-pressure centrifuge fan and operation table. When equip the dust removing equipment, it should consider the practical need. It can select cyclone separator and cloth bag duster at the same time or one of them. In general speaking, it needs to select cyclone separator only for raw material that is large in specific gravity and cloth bag duster for powder and small granule raw materials that is light in specific gravity.
Drying principle:
Boiling dryer is to make use of the clean air after filtered to exchange heat through the heat exchanger to make air increase to certain temperature to enter into the division drum; then it is distributed by valve plate and enters into the boiler while moist material enters into the dryer from feeder. In the action of wind force, material forms boiling in dryer. Heat air contacts completely with material, which strengthens heat transmission. Therefore, water can be separated from material in very short time. This equipment is usually operated in negative pressure.
Heating methods:
Steam, electricity or hot-air furnace can be sued. (It can be supplied as request.)
Installation explanation:
1. Boiling dryer has to use sealing strip to connect each part during installation; and has to use joint sheet to insulate to keep it not leak; or it will seriously influence the effect of boiling.
2. In order to avoid the noise of fan, user may equip the fan in muffler.
3. Cyclone separator, cloth bag duster and fan can be installed in any position as required.
Application:
It is suitable for drying separated granules, such as, raw material of pharmaceutical industry, tablet, tablet of drink of Chinese traditional medicines, plastic resin, citric acid, other powder and granule of chemical industry, powder of drink, corn embryo feed of foodstuff industry and so on. The maximum diameter of raw material to be dried will be 6mm and the best diameter will be 0.5-3mm.
Technical parameter
Parameter
|
Area of bed layer
|
Drying capacity
|
Power of fan
|
Wind pressure
|
Wind volume
|
Temperature of air in
|
Temperature of material
|
Max. energy consumption
|
Occupied area
|
Feeding mode
|
Model
|
㎡
|
kg/h
|
kw
|
pa
|
m3/h
|
℃
|
℃
|
M3/min
|
㎡
|
- filling mode;
- combining filling mode and air conveyor
|
Type-20A
|
0.5
|
20-25
|
11
|
5.5×103
|
3110
|
60-140
|
40-60
|
2.6
|
25×103
|
Type 20B
|
0.5
|
20-25
|
11
|
5.5×103
|
3110
|
2.6
|
20×103
|
Type 30A
|
1.0
|
30-45
|
18.5
|
7.0×103
|
4370
|
5.2
|
35×103
|
Type 50A
|
2.0
|
55-90
|
30
|
7.4×103
|
7540
|
10.4
|
45×103
|